J&J Bagging
Yazoo City, MS

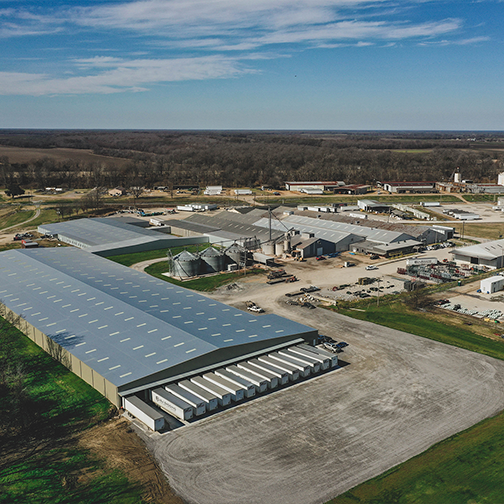
Weighing System Development for J&J Bagging
Summary
J&J Bagging is a fertilizer storage & packing facility located in Yazoo City, Mississippi. The Michelli Weighing & Measurement team recently helped J&J Bagging increase efficiency and decrease safety risks by developing a wireless weighing system that aids in their fertilizer batching operations.
During the batching operation, J&J Bagging employees use front end loaders to pick up & deposit predetermined amounts of ingredients into four hopper scales at the facility. Those ingredients are then mixed into a batch of
fertilizer, which is packaged, and added to a shipment to be sent to end users. For example, the employee may pick up and deposit 50 lbs. of ingredient A, then 150 lbs. of ingredient B, then 300 lbs. of ingredient C into a
hopper. Those ingredients are then deposited into a bag. Several bags are added to a pallet, which is shipped to the end user.
J&J Bagging needed a way to enable employees to accomplish two goals during the fertilizer batching process, without leaving the cab of the front end loaders:
-
- Track the weight of multiple ingredients as they are added to each of the 4 hopper scales
- Tare or “Zero out” the hopper scales between the addition of each ingredient
Features
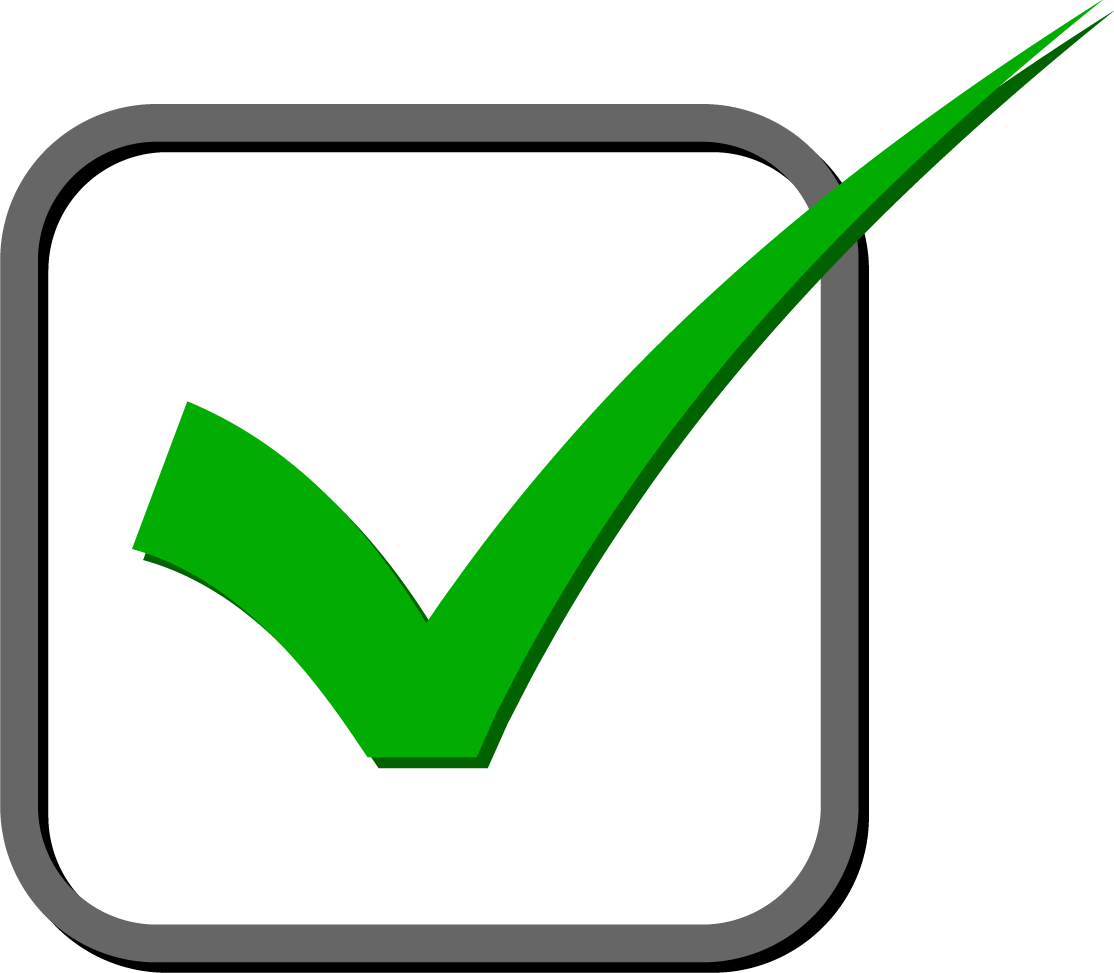
Expandable Solution
To accommodate future growth
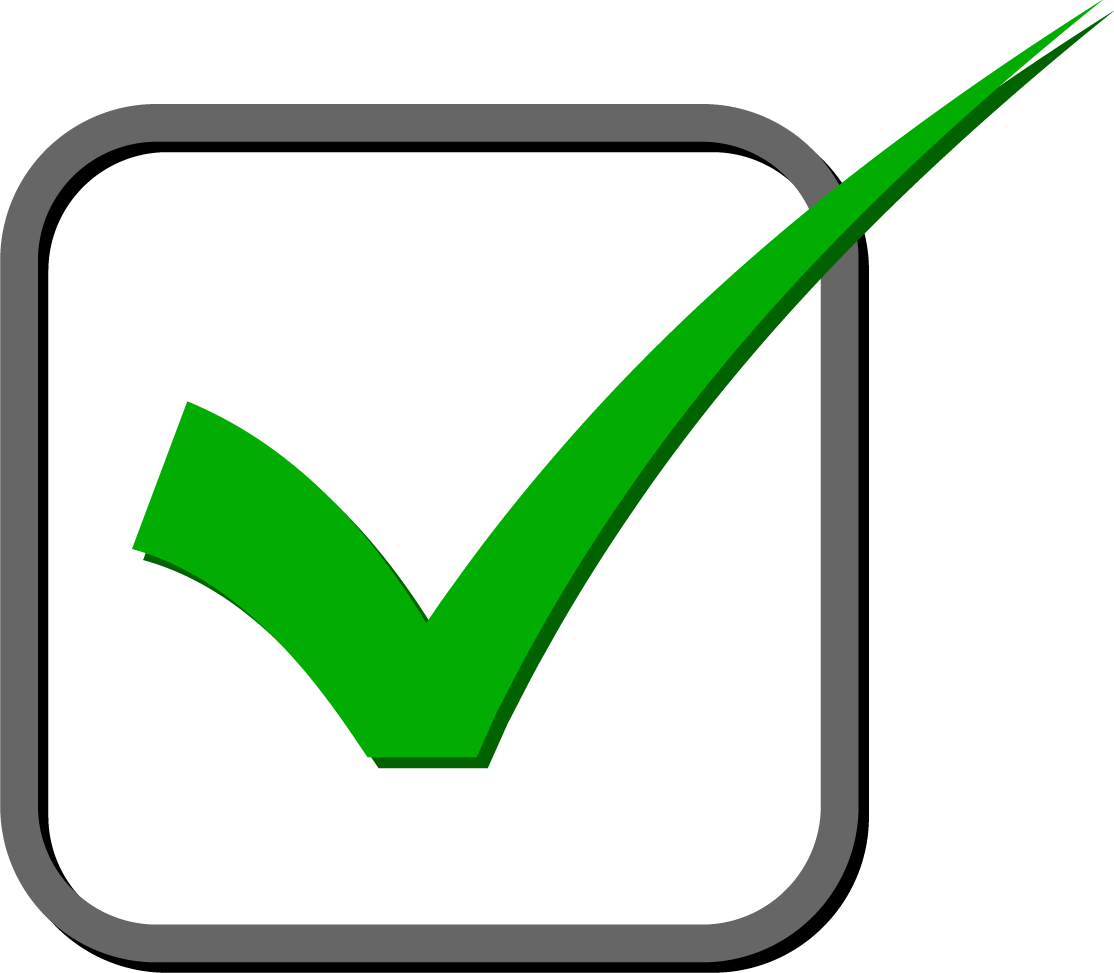
Increased Weight Visibility
To ensure quality assurance both in-cab & from a distance
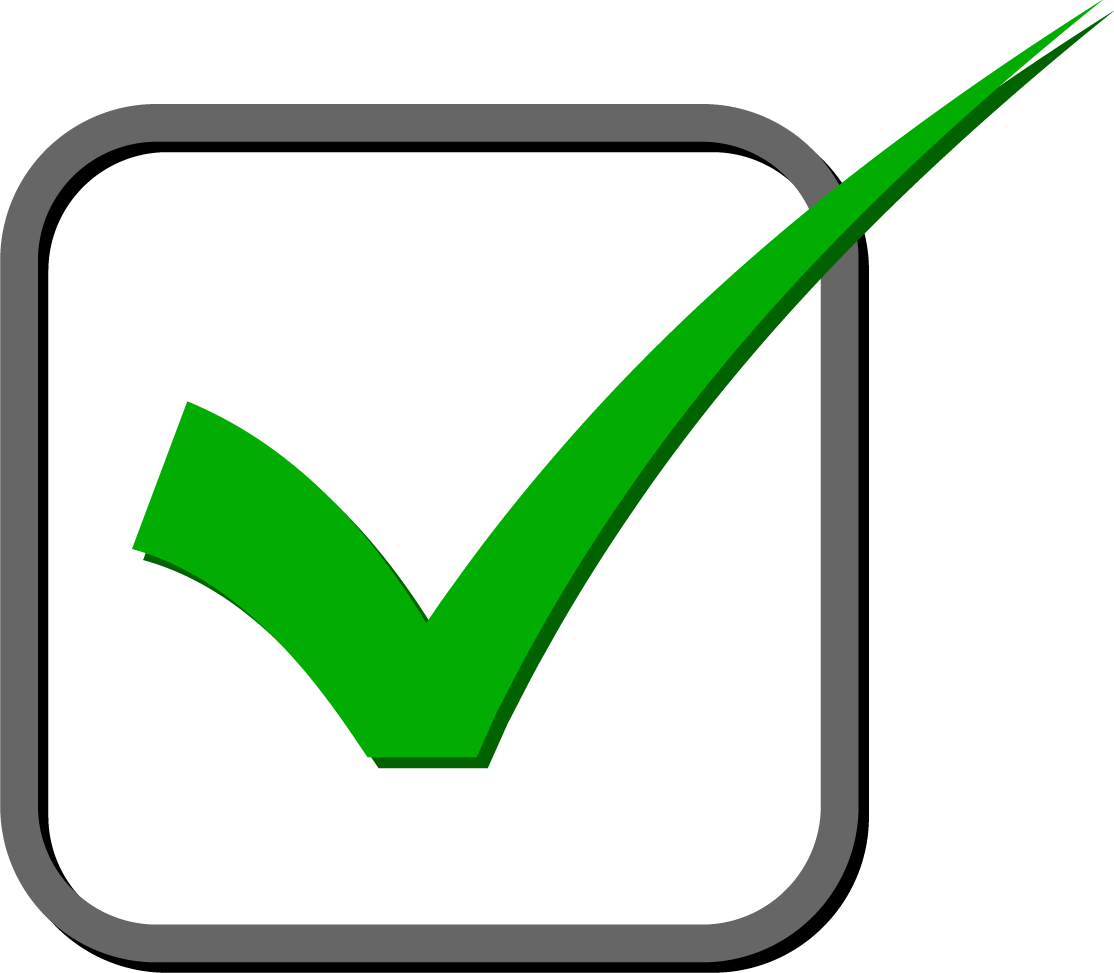
Operator Controlled
To reduce errors
Benefits
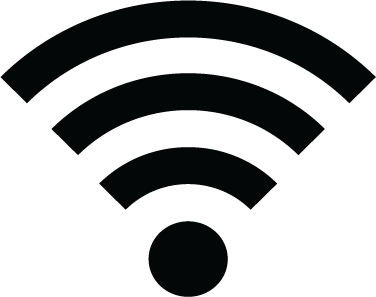
Wireless Solution
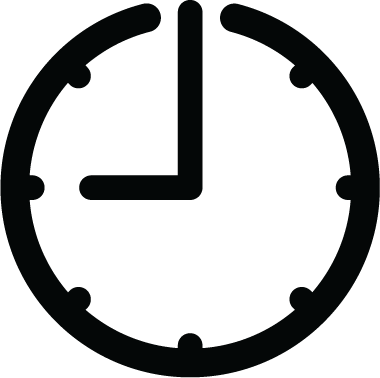
Increased Efficiency
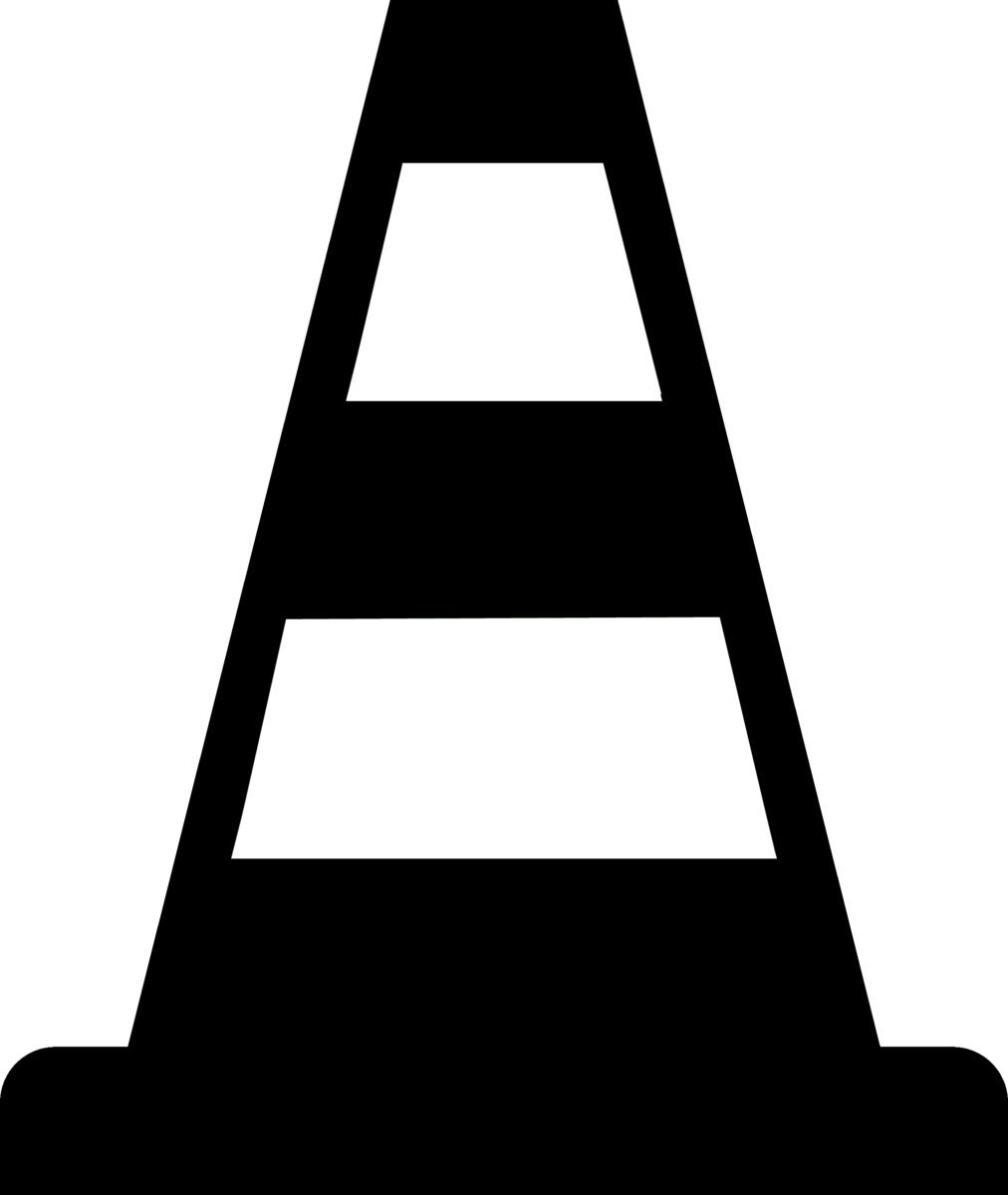
Decreased Safety Risks
Problem
The operator uses the front end loader to pick up a load of a particular fertilizer ingredient, then deposits a predetermined amount of that ingredient into each of the four hopper scales. He needed the ability to view the weight of the ingredient as it is being deposited to ensure the target weight for each batch is being reached. Additionally, he needed the ability to tare each of the four hopper scales in between ingredients to ensure he was depositing the correct amount of each ingredient into each hopper scale to create the perfect fertilizer mix. To do so, the operator previously had to exit the front-loader & walk to the hopper scale to tare or “zero out” the indicator manually, decreasing efficiency & increasing safety risks.
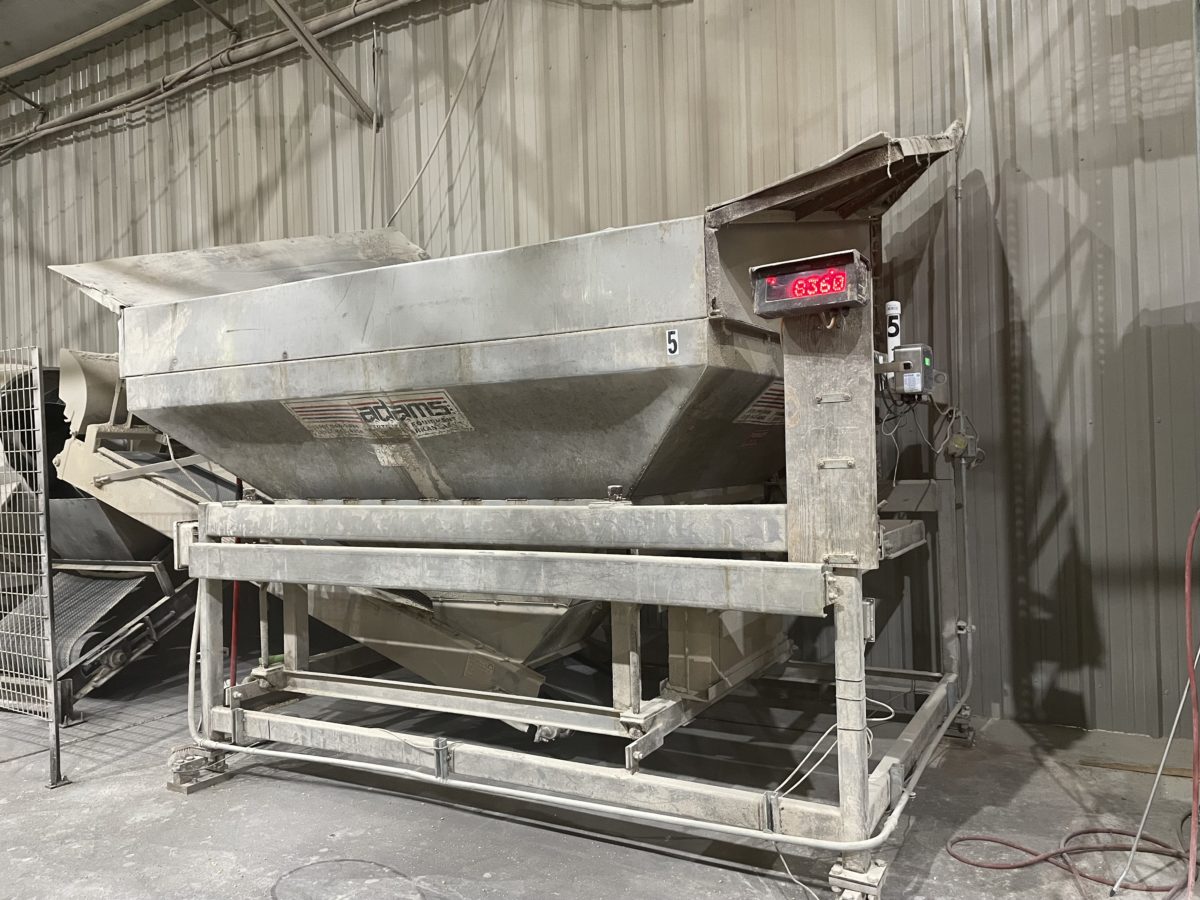
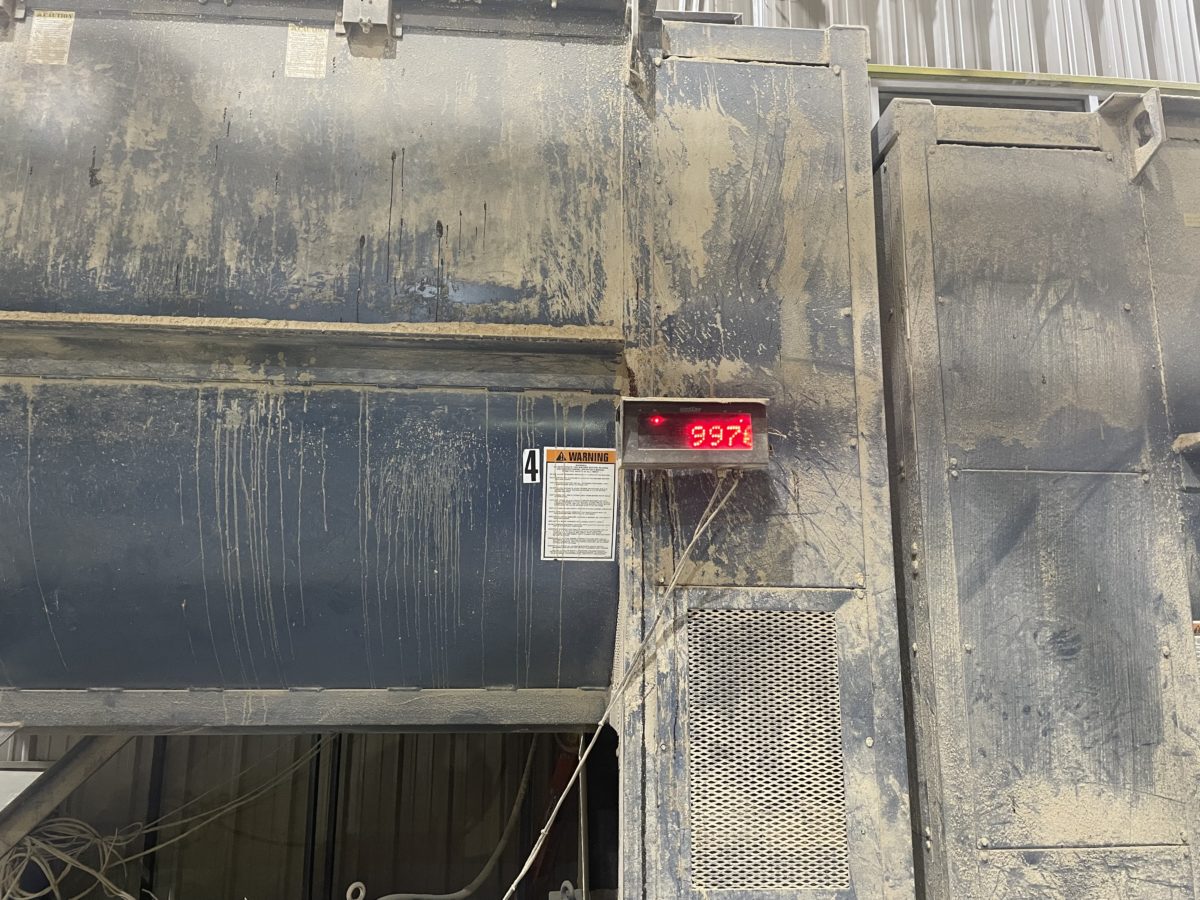
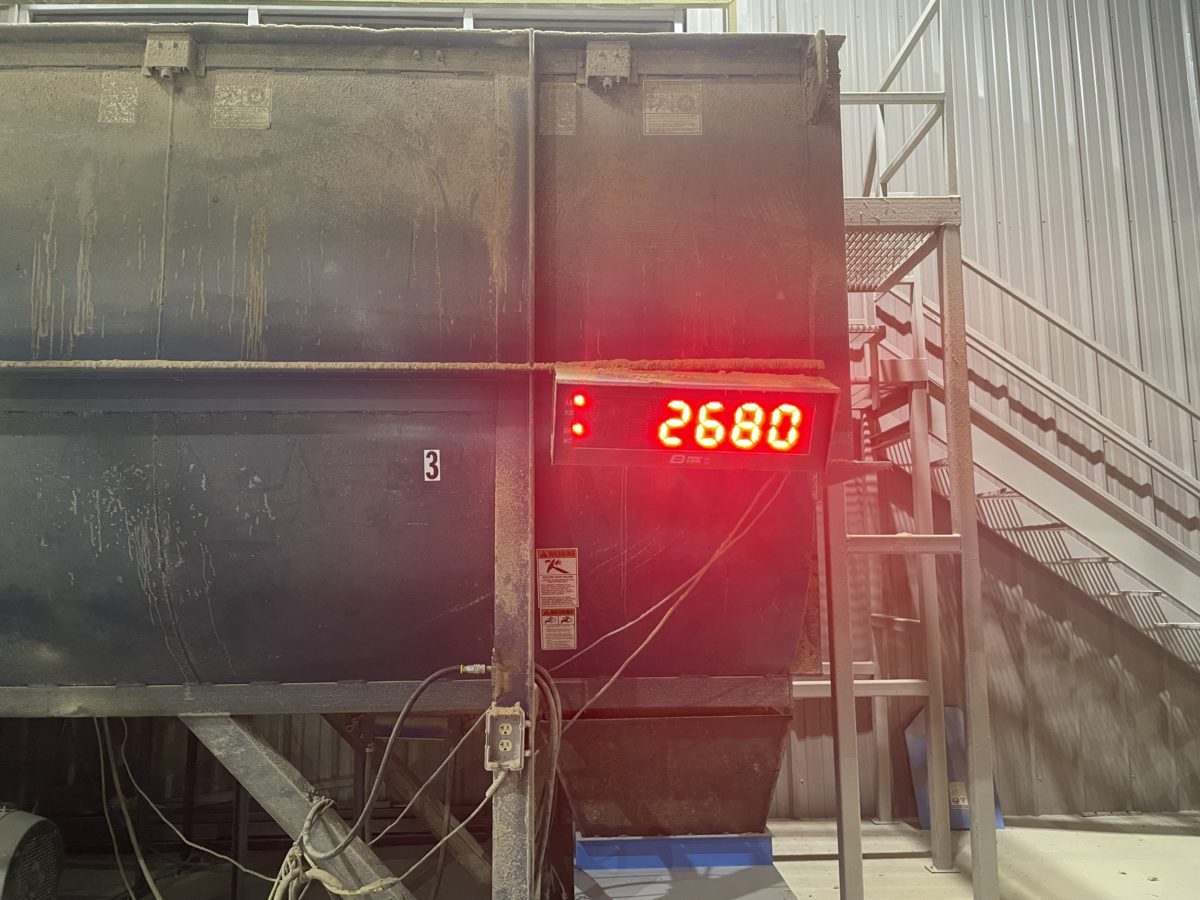
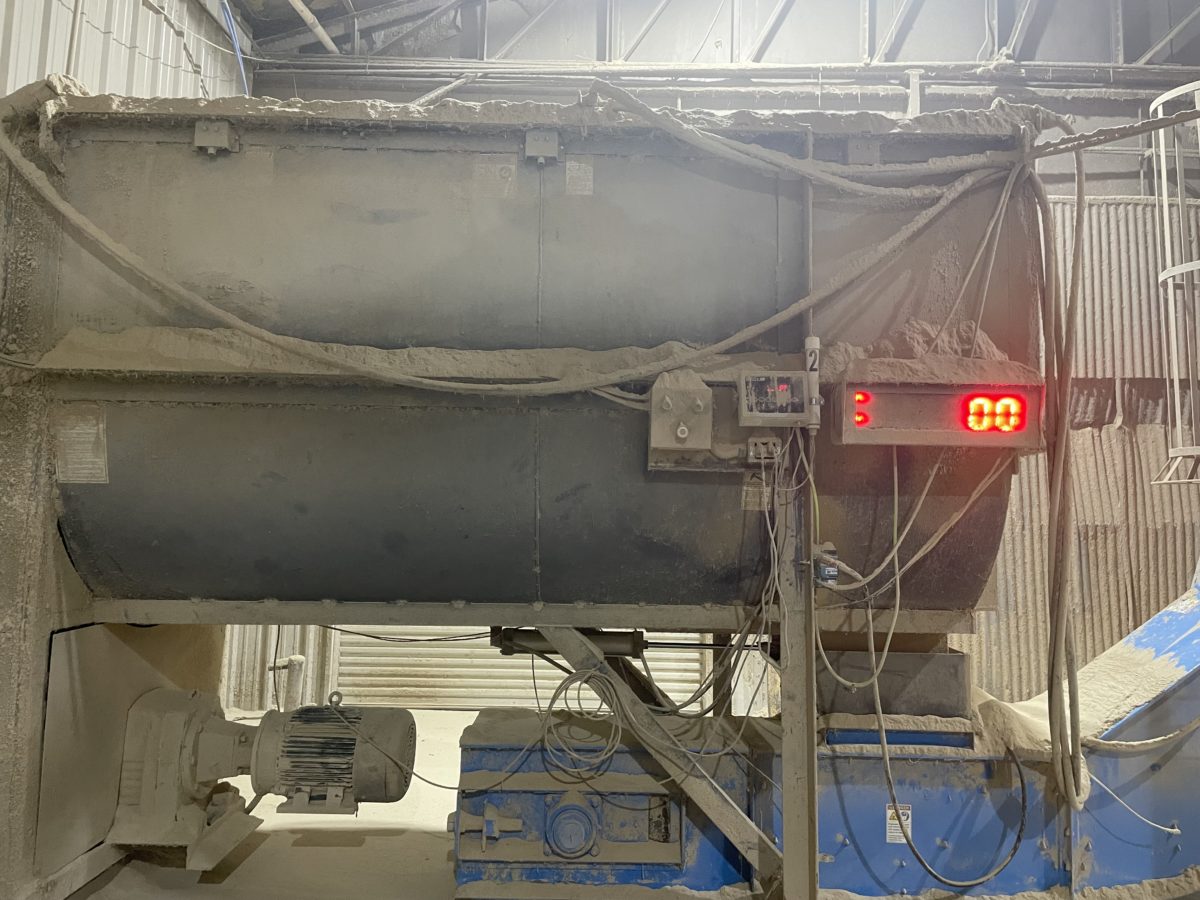
“The customer called to express how happy they were with the new wireless systems”
-J.R. Nickerson, Regional Service Manager
Solution
The solution developed by the Michelli team includes four wireless weighing systems; one for each of the four scales utilized during batching and bagging operations. Along with custom programming, these wireless weighing systems included the following components:
- Handheld indicators – These were mounted in the cab of each front end loader at eye level to allow the operator to keep the relevant information in constant view.
- Remote display LED scoreboards – These enable supervisors to view from a distance the weight of each material as it is being deposited into the hopper.
The front end loader operator now has the ability to switch the information displayed on the “handheld” indicator to distinguish between each of the hopper scales as needed. This feature of the weighing system allows the
operator to pick up a load of ingredient A, and deposit the required amount into each hopper scale.
The J&J Bagging employee can also now tare or “zero out” each hopper scale as needed from the cab of his vehicle. This feature allows the operator to get an accurate weight of each ingredient as it is deposited into the hopper scales, enabling him to monitor the amount of ingredient B he is depositing in real time to ensure the target weight is reached.
This functionality allows the employee to complete the batching operation more quickly, without leaving the cab of the front end loader, saving time while simultaneously reducing the risk of the employee slipping, and the risk of human error. The fact that the solution is entirely wireless also helps reduce safety risks, as there are no wires in the way for the employees to run over or run into during the batching operation.
Contact Us Today
Let us develop a solution that helps you increase efficiency and decrease safety risks.