Should you replace obsolete equipment? Will it help minimize unplanned downtime?
Whether or not to replace obsolete equipment is a decision many companies face each year. Doing so is definitely a great way to minimize unplanned downtime, but is it worth the associated cost? A new equipment purchase may be a significant investment, and it’s worth careful consideration to decide on the best route for your business.
The initial “sticker shock” over the price of new equipment might cause hesitation, or even lead businesses to believe it’s out of the question. The thing is, there are many more factors to consider beyond the purchase price of new equipment. The best way to decide if it would be worth it to replace obsolete equipment is to perform a risk assessment. A risk assessment allows decision makers to compare the risks & cost of maintenance of obsolete equipment with the cost of replacement. We asked the experts at Michelli Weighing & Measurement to weigh in on important factors. Below are some questions to help get you started.
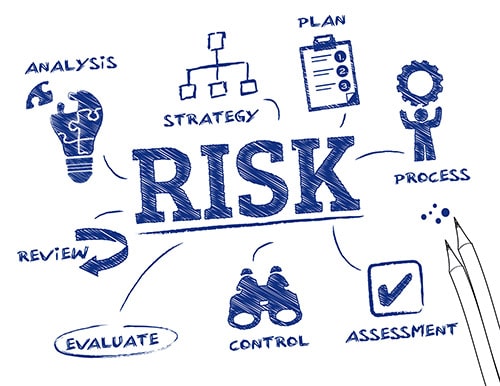
Here are some things to consider when performing a risk assessment on obsolete equipment:
Is this machinery critical to the organization’s operation?
If the obsolete equipment stopped working today, could operations continue without it? If the answer is no, then it’s time to plan accordingly. If the equipment is obsolete, it’s only a matter of time before replacement parts are no longer available. It may also become more difficult to find a service provider that can help with maintenance. Having a contingency plan will help ensure your business doesn’t lose money and time with unplanned downtime while waiting on new equipment to arrive.
Another factor to take into consideration is the amount of money the business would lose each day if the obsolete equipment malfunctioned & was out of service. If this machinery is critical, that amount may be significant. If so, the sooner you put together a contingency plan, the better. Consider this when budgeting for new equipment. It’s important to invest in quality tools, including maintenance costs, to ensure dependability. If this equipment is critical to profitability, choose equipment that can stand the test of time.
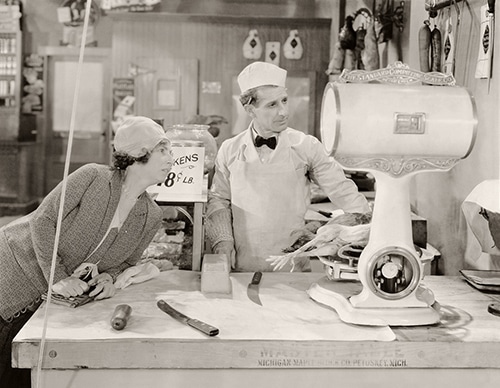
Is the obsolete equipment at a high risk for failure?
Has the equipment in question had any issues in the past? Were those issues recurring? If so, you may already be considering replacement equipment. Oftentimes obsolete equipment is overworked, and even with the best maintenance plan, has reached the end of its useful life. In these situations, the question isn’t whether or not you should replace the machinery, but how quickly can you get the replacement equipment up & running. Remember to consider the current supply chain issues and the time it may take to train staff on the new equipment in this decision.
Is the equipment difficult to maintain or repair?
Does repairing or maintaining the machinery require a significant amount of downtime? If so, how do you work around that? Some organizations schedule planned downtime during the holidays, when most employees might have taken off of work anyway to reduce the monetary loss. Another factor to consider is whether newer equipment might take less time to repair or maintain. If the answer is yes, organizations could cut down on their scheduled downtime, allowing more time to continue operations as normal.
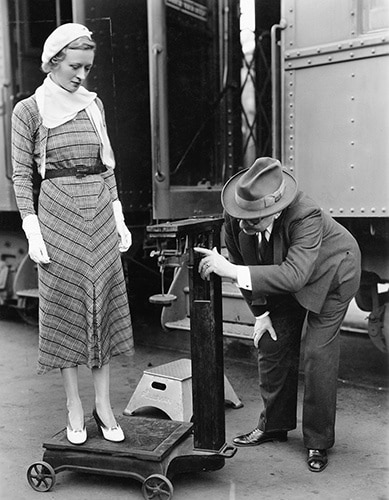
Is the average cost of maintenance and repairs less more than the cost of replacement?
To determine whether the cost of maintenance & repairs on obsolete equipment is greater than the cost of replacement, add all of the prior year’s maintenance & repair costs together. Remember, the cost of new equipment will also include maintenance, but the costs incurred should be less frequent. You can discuss this with your Michelli Weighing & Measurement account manager & ask what type of maintenance plan they might recommend if you purchased new replacement equipment. Lastly, consider the amount of electricity & manpower required to operate the existing equipment. Compare that to the amount that will be required to operate the new equipment. Are the costs lower with the obsolete equipment or the new equipment?
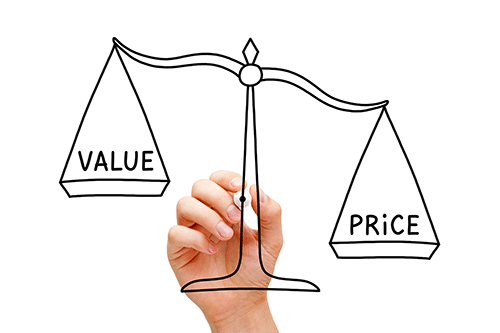
Is support available for the obsolete equipment?
If your equipment requires regular updates to continue to operate, is the manufacturer still offering support? If not, there may be newer replacement equipment & technology available that performs the same functions more efficiently.
Are spare parts available for this equipment? If so, what is the lead time like on these parts? If spare parts are difficult to find, it’s time to put together a back-up plan. First and foremost, order spare parts to keep on hand in the event that the machine goes down. With supply chain issues, it may take much longer to get spare parts than it has in the past. (Read our blog post Stock Spare Parts to Minimize Unplanned Downtime to learn more.)
Is the obsolete equipment safe to operate?
Perhaps the most important factor to consider is whether or not the obsolete equipment is safe to operate. In some cases, older equipment has been recalled due to serious risks that have been uncovered during operation. If the equipment poses any danger to users, it’s definitely time to replace it, especially if that risk is to human life. Newer equipment is held to different safety standards throughout the manufacturing process, and oftentimes contains built-in shut off capabilities to further protect users.
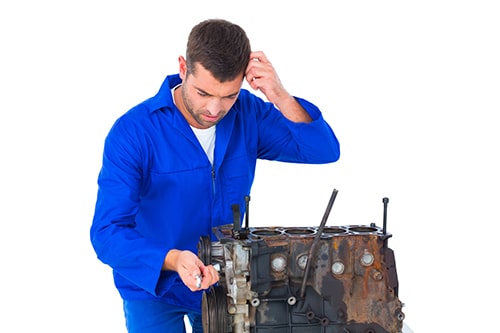
Would Replacing Obsolete Equipment Be Beneficial?
Users should consider whether newer equipment could perform the same function more efficiently, more cost effectively, or more safely than the obsolete equipment. If the answer is no, then your organization should continue to use the existing machinery, even if it is obsolete, for as long as maintenance, parts & support are available. However, if the answer is yes, then it’s time to start planning.
Initially, the cost of new equipment might deter organizations from replacing old gear, but in reality, replacement might cost less than maintenance & repairs. Luckily, Michelli Weighing & Measurement can help. We offer financing to help you get the equipment you need today, while paying over time. Learn more on our financing page.
Remember Preventative Maintenance
Whether or not you decide to replace obsolete equipment, it’s important to set up a preventative maintenance plan. Preventative maintenance helps ensure that all equipment continues to run as expected for as long as possible. It also helps users maintain a firm grasp on when repairs might be required, and when to order spare parts, enabling them to plan accordingly. Lastly, preventative maintenance helps keep equipment operators safe, by giving them a chance to detect any potential issues before a problem arises.
Get Help from Our Experts to Determine Whether to Replace Obsolete Equipment
Our account managers can help you determine if replacement is the right option for you. If keeping your current equipment makes the most sense, we can help you find a maintenance plan to keep your existing equipment running for as long as possible. If replacement makes the most sense, we can match you with the right equipment for your needs & your budget. Contact your local Michelli Weighing & Measurement location today.