Using Quality Control Weighing Systems
Weighing is one of the fastest ways to manage quality control operations. Quality control weighing systems are used to ensure consistency. By weighing products that should be identical, we can quickly identify any anomalies, allowing us to maintain uniformity. These systems normally compare products to a set weight standard. This set standard is referred to as the “target weight” and in most cases includes a “tolerance” to allow for minor variations.
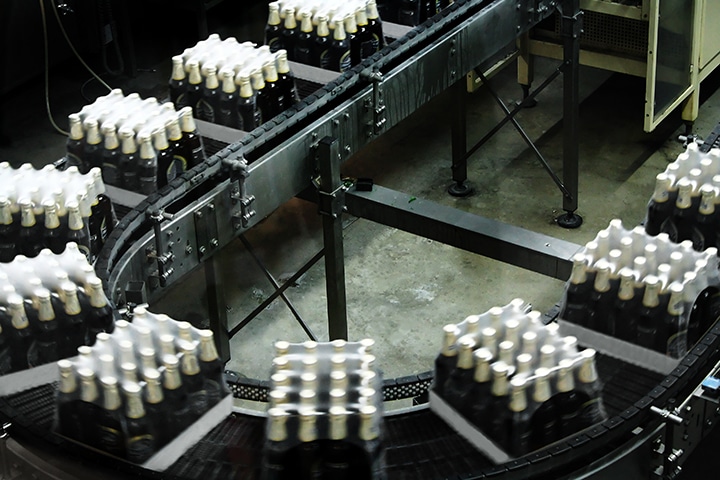
For example, if packages are being weighed and the target weight is 1 lb, the tolerance may be plus or minus 0.5 ounces. So, any packages whose weight registers within 0.5 ounces of 1 lb (between .5 ounces & 1.5 ounces) are still considered acceptable, because they are within the tolerance of the 1 lb target weight. Packages that weigh .4 ounces, or 1.6 ounces would be rejected.
Some quality control weighing systems are automated, while others require human interaction, or at least human monitoring. In some cases, products outside of the target weight range may be kicked off of a conveyor line by a mechanical arm, or they may set off a red light to alert the human workers to remove it from the line.
Quality Control Weighing Systems Used in Filling Operations
In a filling operation, a quality control weighing system might be used to ensure that each bottle contains the correct amount of an ingredient such as dish soap, oil or even cough syrup. Weighing systems are used in dry good factories too, in the packaging of aspirin or vitamins for example.
There are many different types of quality control weighing systems. Some may be used during mixing operations to ensure the correct amount of ingredients is added to a product batch. Still other systems might be used to determine that each cupcake on a product line has received its icing, or the correct amount of cereal has been added to each box.
Quality control weighing systems provide a much more efficient way to ensure consistency. Tools like conveyor scales & in-motion checkweighers make it possible to perform quality control checks based on weight without interfering with other operations. If a product has passed through a quality control weighing system, it is within the target weight range. In some cases, that may be all that is required to maintain consistency. In other cases, humans will need to perform further testing, but at least the first step will have cut down on labor costs & the possibility for human error.
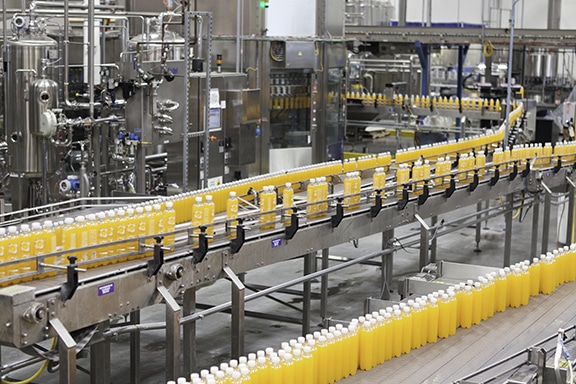
Quality Control Weighing Systems in Production Operations
A production operation might also utilize a quality control weighing system to ensure product consistency. For instance, a factory that produces textiles might wrap their fabric around a cardboard core.
Once the wrapping phase is complete, the factory could use a quality control weighing system to weigh each bolt of fabric as it travels from the wrapping phase to the packaging phase of operations. Doing so would allow the workers to ensure that the correct amount of fabric had been added to each cardboard core without unrolling each to measure the fabric.
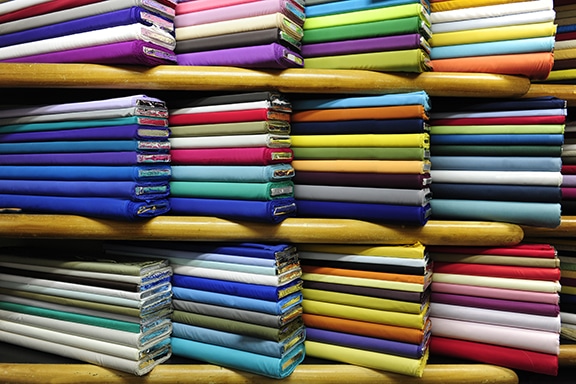
Weighing for Quality Assurance After Packaging
Still other production operations might utilize weighing systems in quality control operations after packaging is complete to ensure each product box contains the correct amount of material. For example, a factory that produces tablets might box the tablet with a stylus, charger & instruction manual. In order to make sure every box contains the correct components, the factory could utilize a quality control weighing system. If the tablet factory utilized a weighing system with a conveyor belt & an automated arm, workers could enter the weight of a complete box (one containing all of the components) as the target weight. Then, any boxes traveling down the conveyor belt that are not within the preset tolerance of the target weight would be rejected, and kicked off of the production line by the automated arm. Using a weighing system would allow the factory to ensure the quality of the product before it leaves the factory, and to do so without disturbing the integrity of the packaging.
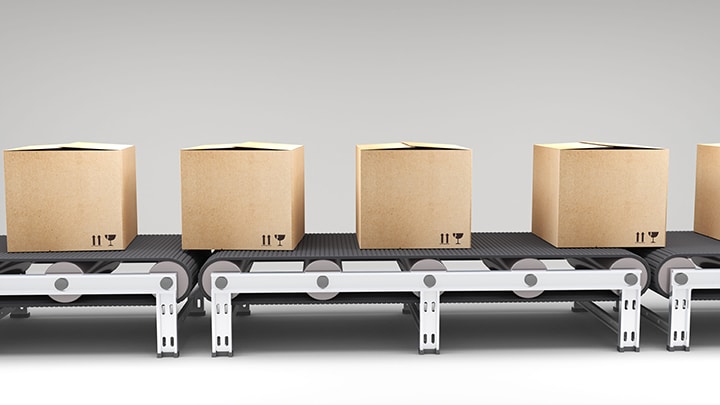
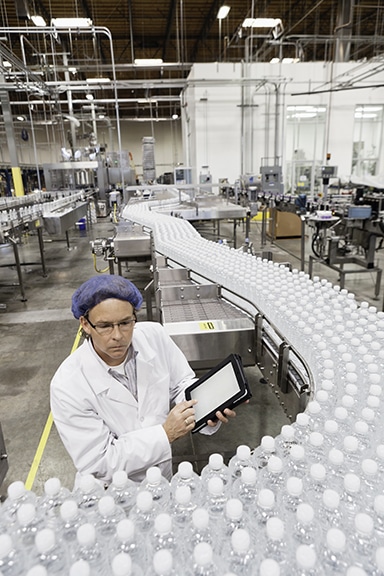
Value Added by Using a Weighing System for Quality Control
Quality control weighing systems help users maintain uniformity by using weight to gauge consistency between products. Obviously, not every quality control check can be based on weight. Some quality control operations must be performed by a human, to make sure each product looks, feels, smells or tastes like it should. Quality assurance operations can contribute to a bottleneck effect, creating long production lines, which leads to higher labor costs & more opportunity for human error.
Many quality control systems still require human interaction to remove the “rejected” product, further examine the product, or to select which random products are pulled from the production line for testing. If any part of the quality control process can be simplified, such as using weight to determine uniformity, it helps alleviate the long production time, efficiency is increased & cost is decreased.
Other Types of Quality Control Systems
Quality control weighing systems are used heavily in sorting operations in the food & beverage industry, during which cuts of meat are sorted & labeled, then sold based on their weight.
Other quality control systems utilized in the food & beverage industry include foreign object detection, which helps to ensure that your product only contains the ingredients it is meant to contain. For example, a metal detector might be used after cereal boxes are sealed to ensure that a loose screw didn’t make its way into your cereal box as the box traveled through the filling stations.
Are you interested in implementing a quality control weighing system in your operation?
Let us develop a quality control weighing system to help you streamline operations & increase efficiency.
Contact your nearest Michelli Weighing & Measurement location to speak with a product specialist today.