Why Create a Calibration Schedule?
A calibration schedule is an imperative part of any quality or safety program. It helps employees and managers ensure that equipment is functioning properly and safely. By creating and enforcing a calibration plan, users can rest assured that the measurements produced by the equipment are accurate. If the equipment has been serviced by an accredited calibration lab, the calibration also provides measurement traceability, which is important for regulatory purposes.
Unfortunately, it’s all too easy to overlook preventative maintenance. Day-to-day operations often seem to take priority over preventative tasks, and calibration is postponed or forgotten. This is a real problem. If precision measurement equipment is out of tolerance, it can produce incorrect measurements, which could be dangerous, or even fatal. A calibration schedule can help users remember to have equipment serviced before it’s too late, and plan downtime accordingly.
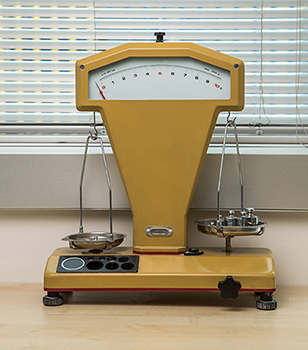
How Often Should you Schedule Service?
Calibration frequency will depend upon a few different factors. The first factor is frequency of use. The more often an asset is used, the more often it should be calibrated. For example, a torque wrench manufacturer may recommend in its user guide that the wrench be calibrated every 5,000 cycles. It’s impossible to say that this equates into “once a year” because individual organizations will use the wrench at different rates. A company who uses the wrench daily should have it calibrated much more frequently than an organization who uses the wrench a few times per month. Also, torque wrench users don’t typically record each time they use the wrench, so unfortunately, the number of cycles between calibrations could be left up to estimation.
Recommended frequency also varies greatly among industries. A general rule of thumb is the higher the risk associated with the use of the instrument, the more often the equipment should be calibrated to ensure it is performing properly. Revisiting our torque wrench example, a wrench used to attach tires to vehicles should be calibrated frequently. An under-torqued tire or over-torqued tire poses very immediate danger to the driver of the vehicle, as well as other drivers on the road. On the other hand, a torque wrench that is only used occasionally to tighten a bolt on a small tank that holds water may require less frequent calibration.
Factors to Consider to Determine Calibration Frequency:
- Do legal requirements dictate calibration frequency?
- Does your company policy dictate calibration frequency?
- How often is the equipment used?
- How high is the risk associated with an improper measurement?
How to Create a Calibration Schedule
1. Create an Asset List
An asset list should include all precision measurement equipment owned by the person or organization. Each asset should be given a unique asset ID. This is often the serial number, or a combination of the serial number and other characters. Each asset should also be labeled as critical or non-critical.
A good way to determine criticality in terms of weighing & measurement equipment is to consider if inaccurate readings produced by this equipment could impact safety or quality in any way. Some organizations also choose to include location in their asset list, which helps ensure each asset is returned to the proper department after service.
2. Determine Calibration Frequency for Each Asset
After creating an asset list, you will need to determine how often each asset should be calibrated. Consider how often the asset is used, and how critical it is to operations. Then, determine if its calibration should automatically recur, or if the instrument could be calibrated as needed, once a quarter, etc. Remember, nothing is set in stone. You can easily revisit the calibration schedule later and increase service frequency if an asset is consistently found to be out of tolerance, or decrease service frequency if an asset is consistently found to be producing accurate measurements.
First and foremost, consider any potential safety risks associated with operating the asset, and how those risks might be increased if the asset is out of tolerance. A calibration schedule should be based on how often calibration is required to prevent any safety issues. Another factor to consider when creating the schedule is the asset’s history. If an instrument was found out of tolerance during its last calibration, or last few calibrations, users should reduce the time between calibrations. For example, if a caliper is calibrated quarterly, and it has been found out of tolerance at the last 2 service appointments, we might recommend that it be calibrated twice per quarter. This will help ensure that the asset is consistently producing accurate measurements.
Lastly, organizations should consider regulatory requirements when determining how often an asset requires calibration. Precision measurement equipment that is considered critical from a safety standpoint may require ISO 17025 accredited calibration at a set interval, given by a governing body.
3. Determine Method of Calibration
Does your equipment require standard calibration or accredited calibration? More often than not, our customers have some assets that only require standard calibration, but other assets that require ISO 17025 accredited calibration. On your asset list, be sure to note the type of calibration each asset requires. This way you don’t waste time or money on the wrong type of service.
Do you require on-site calibration? Or can your calibration service be performed at an accredited calibration lab? On-site calibration may require more planning to ensure your service providers have any required certifications or meet safety requirements to come to your facility.
4. Determine Documentation Method
Determine how you will document your calibration services, including both past and future appointments. Decide where calibration certificates should be stored, and how they should be organized so that they are accessible during an audit. If you plan to keep digital copies of calibration certificates as well, discuss this with your service provider and develop a plan to obtain those. For example, will you need calibration certificates emailed to you after the service is complete? If so, it’s important to relay that information to your service provider.
Some service providers offer asset management software solutions to help ease the burden of maintaining asset records. For example, at Michelli Weighing & Measurement, we offer our customers free access to our TRAC asset management system, which stands for Track Records Assets & Calibrations. Customers can login through our online portal 24/7, where they can quickly view all of their service documents and calibration certificates.
We make it easy to create a calibration schedule and stick to it. TRAC users can see the last service date of any asset, as well as the asset’s history to identify trends. For example, if an asset has been found out of tolerance during each of its last few calibrations, it would be wise to schedule calibration more often to reduce the likelihood of inaccurate measurements. Users can also set reminders in TRAC to help them stick to their calibration schedule. Another option is to establish a Michelli preventative maintenance plan & schedule maintenance or calibration services in advance. A preventative maintenance plan also allows customers to lock in service rates.
5. Establish a Standard Operating Procedure to Maintain the Calibration Schedule
Create a document that outlines the calibration plan & any expectations for your team. Ensure the team has read the document and understands the calibration schedule & procedures. Add this document to future training curriculum for new hires, along with a copy of the asset list & an overview of the calibration schedule.
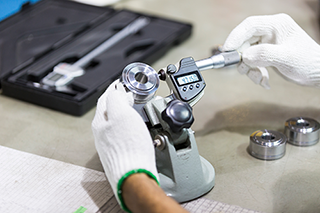
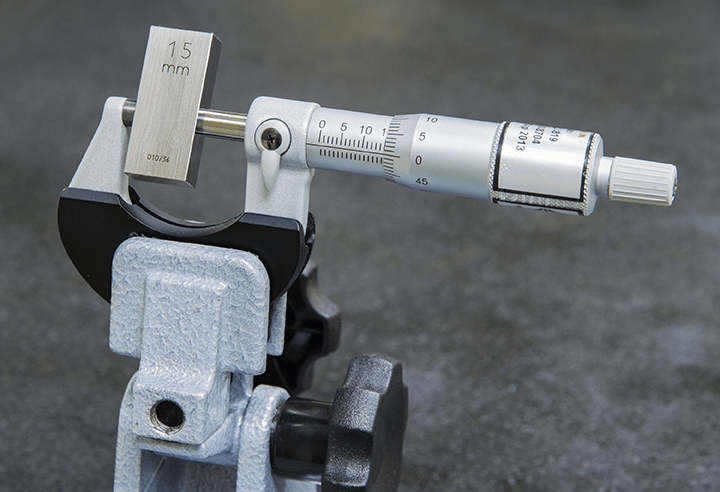
Ensure Accuracy & Maintain Traceability
Creating a calibration schedule may take a bit of time up front, but it’s the smart way to plan for down time. Adhering to the calibration schedule you create helps to ensure that critical weighing & measurement equipment continues to produce accurate readings and is properly maintained. Without a calibration schedule, users rely on memory, or worse, intuition, to determine when their equipment is due for calibration. This is not only an unreliable practice, but also an unsafe one. Ensure accuracy & maintain traceability by creating, and sticking to, a calibration schedule that’s right for your organization.
Let Us Help You Get Your Asset Calibration on TRAC
Contact your nearest Michelli Weighing & Measurement today and let our experts help you create a calibration schedule that you can stick to.