Automated Weighing Systems
Weighing & measurement equipment is used in every step of production. From the time raw material arrives at a production facility, to the time finished goods are packaged & shipped, accurate weight readings are imperative to both quality & safety. Automated weighing systems are used throughout multiple processes during production.
In automated weighing systems, scales are typically added to one or more phases of operations to provide weight checks at multiple points during production. The integration of the scales into the production process allows users to automate certain tasks. The addition of a weighing system can help organizations maximize productivity, increase efficiency, decrease safety risks, or ensure consistency. Let’s take a look at a few examples of automated processes that are enabled by weighing systems.
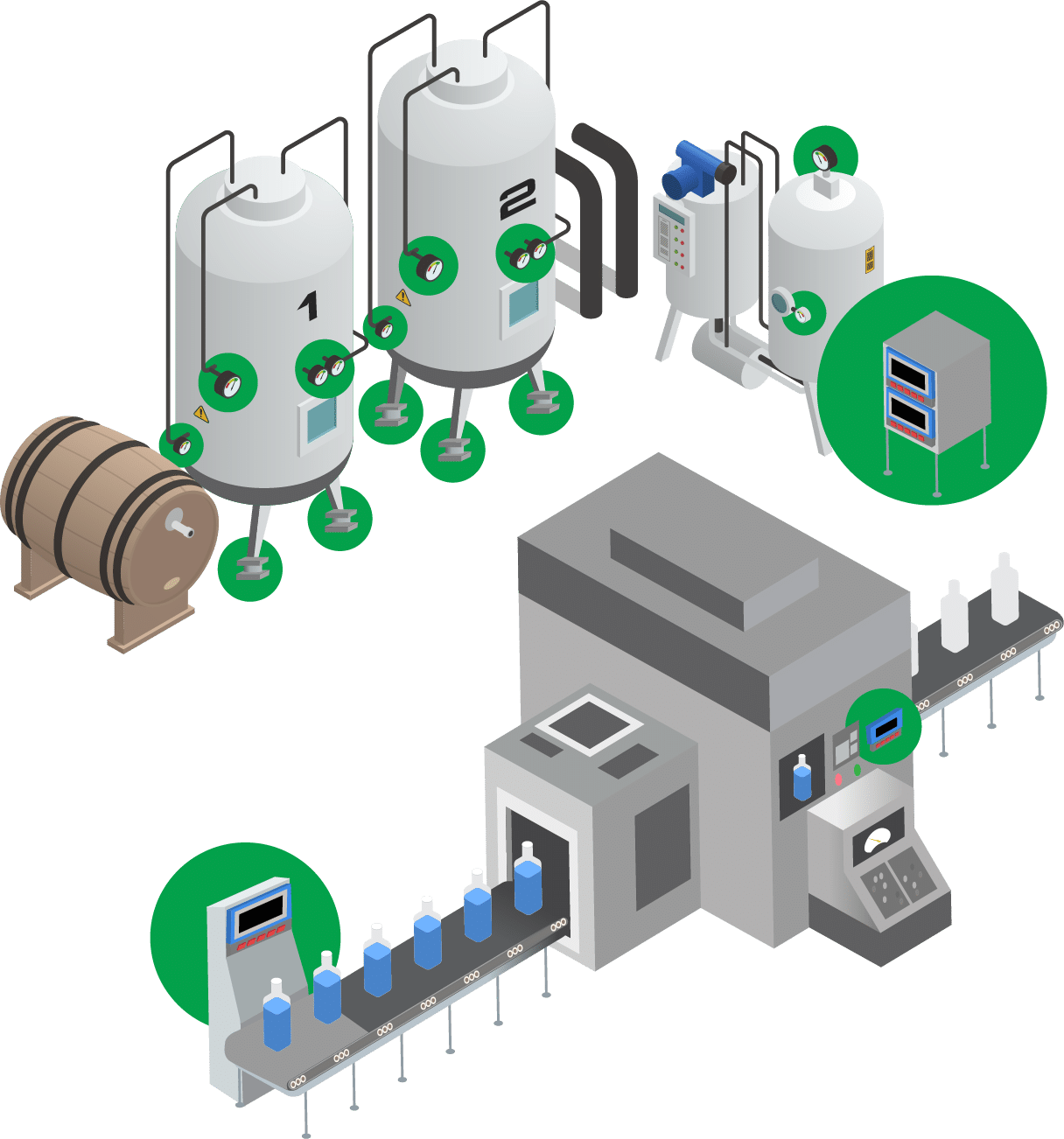
Automated Weighing Systems in the Food Industry
Weighing & measurement plays a crucial role in quality control, safety, pricing & transportation of food. Let’s examine a poultry processing plant to get a better idea of how automated weighing systems are used in the food industry.
Oftentimes, an automated weighing system is used after the poultry products have been packaged, but before they are boxed up & packed for distribution. Think of a pack of chicken thighs. Once the chicken has been placed on a tray & wrapped, it is sent down a conveyor belt. Embedded within the conveyor belt is a scale. Michelli Weighing & Measurement can program that scale to recognize a target weight range. Items moving over the conveyor belt scale that are within the target range will pass, which is indicated by a green light, while objects outside of the target weight range will fail, which is indicated by a red light.
For instance, let’s say that a conveyor belt scale in a poultry processing plant has been programmed with a target weight range of 1-2 lbs. Packs of chicken thighs will be sent down this conveyor belt, and as the packaged chicken thighs run across the conveyor belt scale, a green light will show if the package is within the target weight range of 1-2 lbs. If the package passed the test, it will continue down the conveyor belt to be labeled, then packaged for shipping.
If a pack of chicken thighs runs across the conveyor belt scale and it weighs .5 lbs, a red light would flash, signifying that the package was not within the target weight range. This would trigger an automatic “arm” to swing out and change the trajectory of the underweight pack of chicken thighs. This package would be rejected and pushed onto a separate conveyor belt so that it isn’t labeled & shipped.
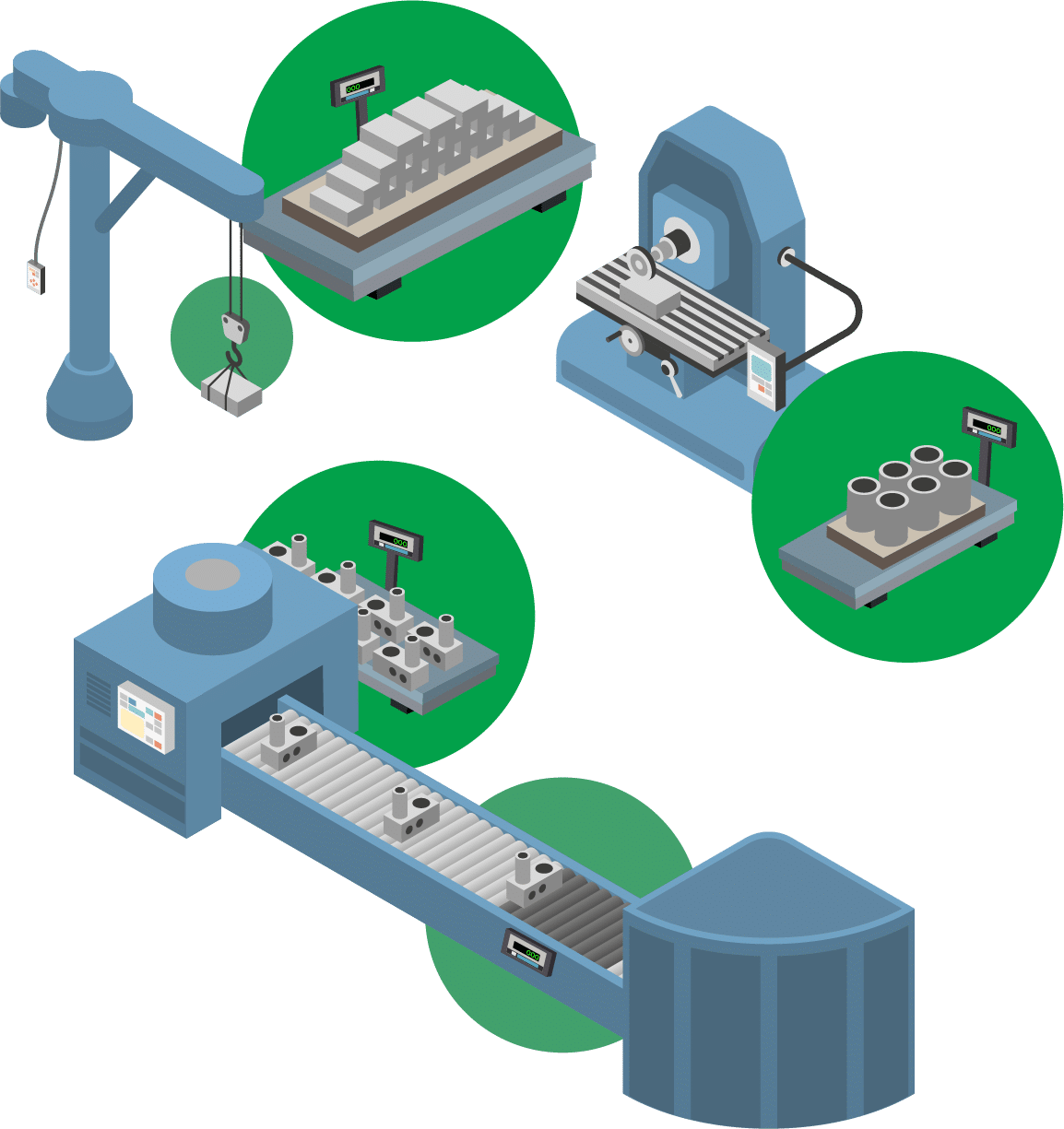
Automated Weighing Systems in Manufacturing
In manufacturing, automated weighing systems are used to increase efficiency and ensure quality control. For example, a factory that produces nuts & bolts might use an automated weighing system to make the quality control process more efficient than a human worker counting bolts prior to packaging.
Imagine that the factory sells bags of bolts, with 10 bolts to a bag. Michelli Weighing & Measurement can get a sample weight of 10 bolts, and a sample weight of 1 bolt. Then we can determine a target weight range. For example, if each group of 10 bolts should weigh 5 ounces, then 1 bolt weighs .5 ounces. We know that the target weight range is 4.6 ounces-5.4 ounces. If a group of parts moves over the scale and it weighs less than 4.6 ounces, it may be missing a bolt. If a group of parts moves over the scale and it weighs more than 5.4 ounces, it may contain an additional bolt.
Groups of bolts that pass the quality control test would pass over the scale & continue down the conveyor belt to be packaged, then forwarded on to shipping to be sold. Groups of bolts that are rejected when they pass over the conveyor belt scale would be sent down a separate line of the system, where they could be collected & recycled or discarded.
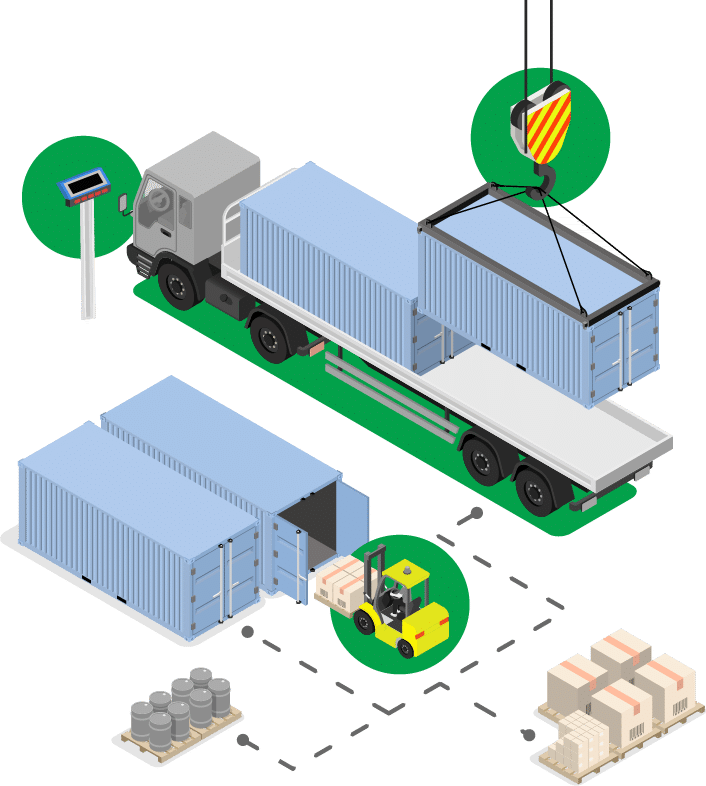
Automated Weighing Systems in Transportation & Logistics
The last phase of manufacturing is getting the product from the producer to the consumer. Automated weighing systems can help with the transportation & logistics step as well. Imagine that the poultry plant needs to get boxes of packaged chicken thighs onto a refrigerated truck, then from the poultry plant to the grocery store as quickly as possible. The refrigerated truck needs to make sure it is within the DOT weight regulations as it leaves the plant. If the truck is underloaded, the plant is losing potential product sales & should add more cargo to make the most of the shipment. If the truck is overloaded, safety & regulatory concerns enter the equation. An overloaded truck is dangerous to the driver & other drivers, and could result in a wreck or a ticket, leading to higher insurance rates.
In order to prevent underload or overload, the trucks need to be weighed as they leave the poultry plant. If the plant has 1 truck scale, but 100 trucks leaving that day, there could be problems. The plant could utilize an automated weighing system to ensure that each truck was within target weight. Michelli Weighing & Measurement could program a target weight range into the scale, so that if the truck was within that range, a green light would flash, signaling the driver that he was within the legal limit & ready to go. A yellow light might be used to signify that a truck is underweight, while a red light might be used to signify that a truck is overweight. This way, the driver would never have to leave the cab of the truck, and could continue on his way if his weight was within the target range. That same automated system could also capture the truck’s weight, a picture of the truck’s license plate, and the date/time of departure. That information could be used to populate a spreadsheet, allowing the scale operator to determine how much inventory left the plant in a certain time period. This information can also be used to determine productivity, profitability & opportunities for growth.
Weighing Systems Make Production Easier
Every stage of production relies on weighing & measurement. Automated weighing systems help to facilitate faster packaging by freeing up human employees for more skilled operations. In quality control settings, automated weighing systems provide a standard of measurement, then automatically decide which products meet that standard so that consumers never receive a sub-par product or the incorrect quantity of a product. Automated weighing systems also help facilitate transportation of finished goods, to make sure that products leave the factory & arrive to the sale venue as quickly & safely as possible. These tasks could be performed without the use of a weighing system, but it would greatly decrease efficiency, as both the amount of time required to complete each task & the possibility of error would greatly increase. Automated weighing systems help facilitate production by making the process as quick, accurate & painless as possible.
Learn How an Automated Weighing System Could Help You
Contact us today to learn how an automated weighing system could help you increase efficiency & maximize productivity.