Wireless scales are an important part of modern-day industry that are sometimes taken for granted. Given the widespread availability of wireless technology in the modern era, it’s easy to forget that not so long ago, wireless solutions were not readily available. Wireless technology has greatly increased efficiency and enabled convenient data transfer. It’s hard to imagine life without wifi, cell phones, or other wireless solutions now. How did wireless solutions evolve? Let’s examine how we got here.
How Wireless Scales Came to Be
If you work in an industrial setting long enough, it will happen. You will need to get data from point A to point B, and even though points A and B are tantalizingly close, you’ll realize there is no way to run a wire. Maybe point A is in the middle of a busy shop floor, or a busy parking lot, or on the other side of a state highway. Trenching is either prohibitively expensive or forbidden, overhead is impractical, going around means hundreds of meters of cable if it’s possible at all. Maybe point B isn’t even in a fixed position, being battery powered and moving around as the job changes. The only way to make this work is to use radio.
Sometimes the equipment manufacturer has attempted to solve this challenge for you. For example, many crane scales have built-in radio systems and standard handheld wireless controllers that will display the weight and allow you to control things like zero, and peak reset. These systems aren’t cheap, but they work pretty well. We know this because these products are popular, and that wouldn’t be the case if they didn’t work.
But then sometimes it’s more mundane. Perhaps a forklift or truck driver needs to trigger a print from the driver’s seat. Maybe there is a kiosk that plays an imperative role in operations that gets moved around a work yard as inventory ebbs and flows. Imagine there is a scale is on one side of an impassable obstacle, and the scale house is on the other. Transmitting data in industrial settings would normally be done with a wire, and equipment is designed with that in mind. However, these situations and others like them have been the catalyst for development of wireless scales.
The Problem With Primitive Wireless Solutions
Over the years, a succession of products have been developed to help with this issue. Nearly all of these solutions had a few things in common:
- They were targeted at moving serial data across the radio bridge.
- They weren’t really designed or made by the industrial equipment manufacturer; they were generic products from companies specializing in data transport and conversion.
- The industrial equipment manufacturer might support them, but that support was never at the level they could offer for the stuff they made themselves.
Since these products weren’t designed for any particular purpose, they were trying to be all things for all applications. Since they were meant to be transparent to an application that expects a wire, they had no way to report trouble on the wireless link to the hardware they were connecting. You can get away without error checking on a wired link but there are a lot more things that can go wrong over radio. This meant you had to come up with your own scheme to make sure that every important message was actually received and intact before moving on to more traffic.
All in all, none of them ever worked very well.
Wifi Enters the Industrial Scale Realm
A better solution, which became practical when scales started popping up with ethernet ports, is to use a network link and convert it to wifi. This actually works pretty well if ethernet is an appropriate medium for your data. Wifi traffic is automatically error checked and retransmitted if it’s not intact. Some scales even provide a function you can call to make sure the link is good. Just as you can send data almost anywhere with appropriate network routing, you can send it through the air with inexpensive commodity bridges and routers.
But there is trouble in wifi paradise too. TCP, the usual transport protocol for “serial” data over ethernet, isn’t suitable for continuous or critical low-latency data. Their needs to be a hotspot which you need to join, and you need to verify that the connection is intact. In some applications you will cross paths with IT department people who don’t want anything on their network that they can’t control themselves. Configuring a wifi system from scratch can be dauntingly complex and confusing. Hotspots are always a tempting target for hackers and the curious. And if your application is giving the truck driver a print button, putting a whole computer and wireless router in the cab can seem a bit overcomplicated and expensive.
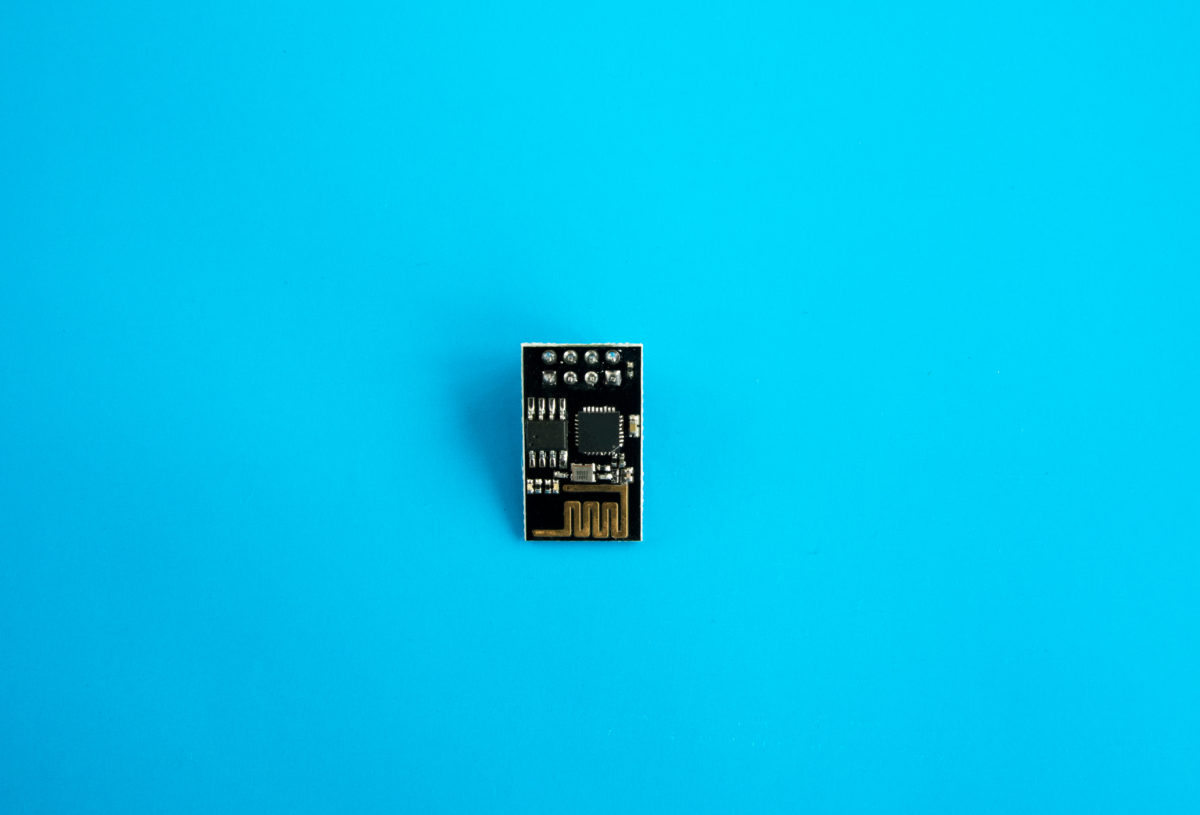
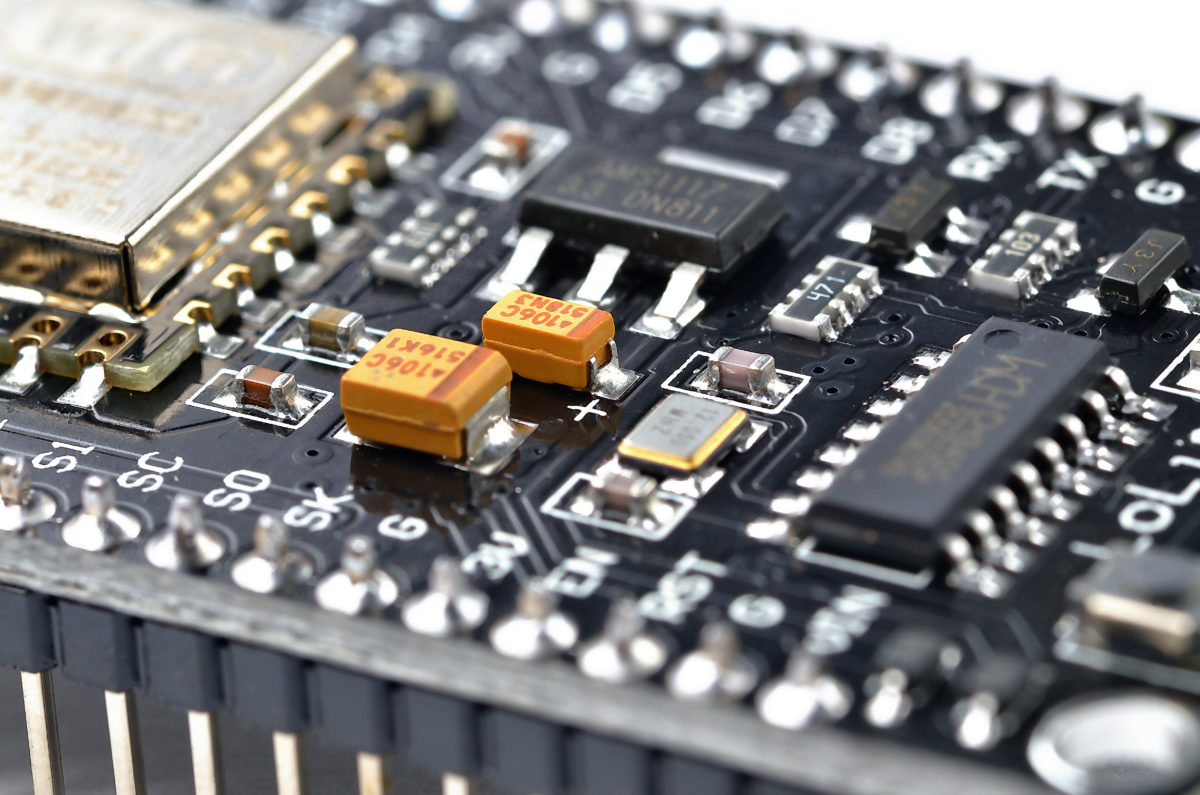
Espressif Systems Enters the Development Space
That leaves us with a solution that is exotic, but in my experience also the least expensive, most versatile, and most reliable: Rolling your own.
Before 2015 this approach wasn’t too practical either. At that time the smallest and cheapest embedded system capable of wifi was made by Texas Instruments; it was a circuit board the size of a credit card. The development tools for programming it cost several thousand dollars to properly license. But in August 2014 there were rumors swirling in the hobbyist community of a new product coming, a single chip solution which put both the radio and an embedded computer on the same silicon chip. In October Espressif Systems made their Software Development Kit (SDK) freely available, and when ESP-01 modules (the first of many reference form factors designed by Espressif and manufactured by many third parties) it was smaller than a postage stamp and cost effective to produce.
According to their website, Espressif “drives AIoT development with complete MCU based solutions with integrated Wi-Fi and Bluetooth connectivity”.
The ESP8266 and the more powerful ESP32, which came out later, aren’t simple radio converters; they are computers that you have to program. But if you’re using wireless of any kind, you’re probably writing some software anyway to contend with data loss and corruption. You may need some other hardware to drive relays. The ESP modules can either join an existing network or put up their own private hotspot. They can do all kinds of more complex functions, as well as just sending data back and forth. They even have a proprietary set of functions that use the wifi radio hardware to send data back and forth point to point without using a network or hotspot.
If you have ever used anything that considers itself a part of the “Internet of things” there is a very high likelihood that there is an Espressif ESP chip inside.
The Future of Wireless Scales
Espressif and the hobbyist service industry have produced a continuous stream of new modules and products and programming tools over the years. Today you can get self-contained modules with LCD screens, buttons, touchscreens, and USB plugs, so you can give that truck driver on the scale a kiosk with both a print button and verification of what he’s recorded.
The original SDK was a bit complicated and hard to use, but within a few years, you could program an ESP in a variety of languages, and some with easy-to- install development systems. The ESP line enabled software development for smart wireless scales.
Wireless scales will continue to be imperative in industrial settings in the future, just as they will continue to evolve. Wireless scales not only allow users to transmit data when running physical wires is impossible, but it also enables users to quickly determine where data is being lost if the radio system fails. This was one of the big problems with those older radio systems. But when the radio relay within the scale is itself a computer, it can tell you what you need to know through another channel, like a display. That feature enables wireless scale users to determine what the issue is and correct it quickly. This capability makes wireless scales much more attractive and practical today than they ever were in the past.
Interested in a Wireless Scale?
Contact your local Michelli Weighing & Measurement office. Our experts can help you find the right weighing solution for your application.