Conditions That Affect Scale Accuracy
Why is scale accuracy important? Portable and in-ground scales are essential tools for commercial vehicle operators to determine axle, axle group, and Gross Vehicle Weight (GVW) in order to comply with regulations and avoid costly overweight citations. The accuracy of these scales can be affected by a number of factors, including proper setup for portable weighing, and site conditions for in-ground scales. In this article, we will discuss how level vs. non-level axle groups affect weighing accuracy for portable scales, and how to optimize performance and accuracy of in-ground scales, like Intercomp’s LS-WIM™ Axle Scales and Strain Gauge Strip Sensors. Additionally, we will cover the importance of regular maintenance and calibration of these scales to ensure accurate measurements throughout their service life.
Portable Vehicle Scales
How Level vs. Non-Level Axle Groups Affects Weighing Accuracy
Portable truck scales allow transport operators to cost-effectively monitor vehicle weights almost anywhere. Commercial vehicle operators can use portable wheel load scales to determine axle, axle group and gross vehicle weight (GVW). When using wheel load scales, it is advised that an axle group (axles within 10 feet, or 3 meters) be on the same plane. This means all axles in a group, including dual, triple and spread axles, should be at the same level as the axle on the weigh pad, either supported by another scale pad or a solid object.
The potential for inaccurate readings increases when axles within an axle group are not level during weighing. To mitigate these effects, placing scales under each wheel of axles within 10 feet (3 m) of one another is recommended.
During testing of various scale models, an FHWA Class 9 five-axle truck was used to compare variation when utilizing one and two pairs of portable wheel/axle scales. The truck had a GVW of 64,860 lb (29,420 kg) – measured by a full-length, certified in-ground scale.
On a level, paved surface, the same truck was weighed using Intercomp’s NTEP-Certified PT300™ scale pads, which are two 3-inches (76 mm) high. The result was a GVW variance of 5.7% and 5.3% from the in-ground truck scale during two separate weighings. In addition, a single pair of Intercomp’s NTEP-Certified LP600™ pads, which are 1.5 inches (38 mm) high, produced a 3.8% GVW variance.
Using four PT300™ scale pads, enough to support the four wheels in both tandem axle groups, the average deviation among the groups was within the 1% rating when compared to the full-length truck scale. Weighing axle groups with one pair of scale pads displaces downward force that a scale would otherwise register. Similar errors occur when attempting to use pads of different heights, also negating the 1% accuracy rating.
The errors become significant as gross, axle group and axle weights approach permissible limits. For example, a truck loaded to 80,000 lb (36,000 kg) could be off between 3,200 lb (1,500 kg) and 4,800 lb (2,200 kg), increasing the potential for costly overweight citations and the promotion of unsafe vehicle operation.
Portable levelers and ramps allow collection of axle weights and Gross Vehicle Weight (GVW) using only two scale pads. The levelers and ramps keep various axle groups on a level plane when crossing the scales. Levelers can also enable more efficient throughput by making it easier to drive on and off the scales.
When all axles in an axle group are weighed on a level plane, each of Intercomp’s portable truck scales are accurate within 1% of applied load.
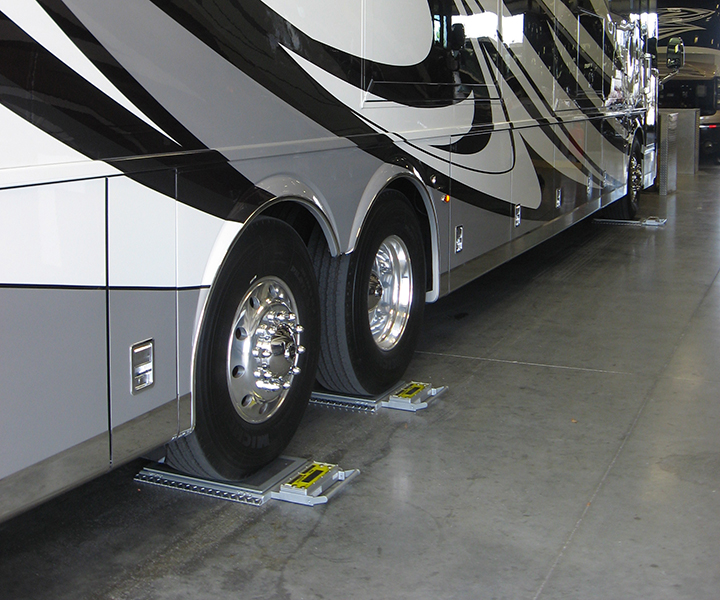
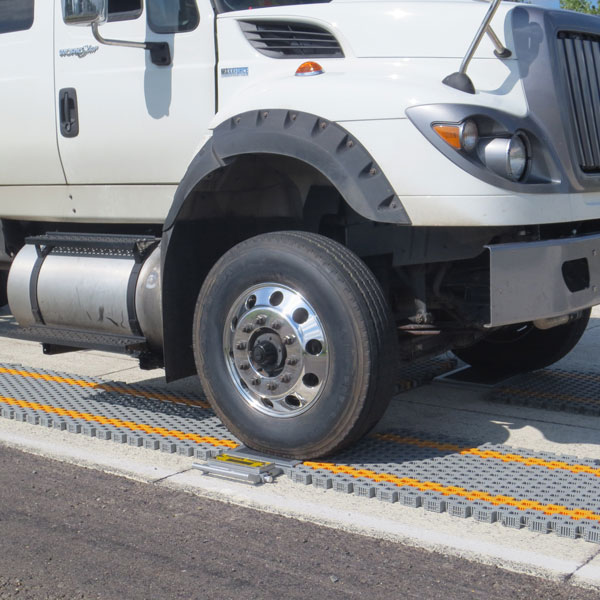
In-Ground Scale Accuracy
WIM site conditions to optimize performance and accuracy of LS-WIM™ Axle Scales and Strain Gauge Strip Sensors
Intercomp’s LS-WIM® In-Ground Axle Scale systems and Strain Gauge Strip Sensors provide a solution to accurately weigh trucks, trailers, or any other type of wheeled vehicle quickly and efficiently. The performance of any WIM system depends upon site conditions to provide a smooth and flat approach to the LS-WIM™ Axle Scales or Strain Gauge Strip Sensors. Recommendations for approaches to a WIM site are dependent upon the anticipated speed that the site will experience. If higher speeds are expected, longer approaches are required. Where speeds are slower, shorter approaches may be acceptable. The length of the vehicles that will be weighed also affects the approach and departure distances. The approach and departure must have enough space for the longest trucks to maintain a constant speed while crossing the scale or sensors. Therefore, optimizing WIM system performance begins with site selection and construction, and continues with ongoing maintenance.
When it comes to selecting your install site, curvature, gradient, and cross slope are three crucial measurements. Whatever horizontal curvature, or bend, there is in the approach should allow the truck, and the trailers it is hauling, to straighten out before crossing the scale or sensors. A gradient that does not exceed 1% is recommended for ideal performance. Also, the truck should not be ascending or descending during the weighing process. Cross slope (lateral slope) should not exceed 1% for ideal performance, but 3% or less is considered acceptable. Basically, you want your approach to be as straight and flat as possible. You don’t want the truck to be turning, ascending, descending, or leaning as it crosses the LS-WIM™ Axle Scale or Strain Gauge Strip Sensors.
The texture of the surface area surrounding the scales or sensors also plays a role in optimizing scale accuracy. The surface of the paved roadway should be smooth before sensor installation, and maintained in a such condition.
It is important to provide and maintain an adequate pavement structure and surface smoothness to accommodate the LS-WIM™ Axle Scales and Strain Gauge Strip Sensors throughout their service life. Installing and maintaining the Weigh-In-Motion scales and strip sensors in accordance with the recommendations of the system vendor will ensure the highest scale accuracy and strongest performance for an in-ground WIM system. Refer to local or regional standards and regulations for specific guidelines on pavement material, structure and surface conditions, or site performance requirements.
Several standards exist that define WIM site conditions to optimize performance and scale accuracy. OIML R134, ASTM E1318 and COST 323 are examples that set forth a number of site condition requirements to be followed for accurate WIM system operation. For complete WIM site condition details, refer to the specific standard in effect for the site location (region).
Maintenance and Calibration
Scales and measurement equipment require regular maintenance to ensure they continue to perform reliably and accurately throughout the life of the product. Regularly scheduled maintenance and scale calibration services are a simple and cost-effective way to keep your weighing and measurement devices operating properly. Rather than reacting to unexpected downtime with expensive emergency repairs, routine maintenance plans allow you to plan and budget for maintenance in advance, limiting unexpected problems or unplanned logistical delays.
Having your scale or measurement device calibrated by a reputable service provider is a reliable, accurate and cost-effective way to ensure your equipment is operating at its best. This also means your weighing equipment is calibrated to exacting industry standards, and is done so by highly-trained factory personnel.
In an accredited metrology laboratory, technicians calibrate your scales with state-of-the-art calibration instrumentation, traceable through NIST or other recognized National Metrology Institutes. Certificates of calibration are provided for all services, and are kept on file for future reference. Michelli Weighing & Measurement customers also receive free access to TRAC, Michelli’s asset management system that allows customers to access calibration certificates & service records online for free. Contact your local Michelli Weighing & Measurement team today to learn more about Intercomp’s portable and in-ground scale options, as well as the best ways to maintain scale accuracy in your environment.
The above post was provided by Intercomp. For over 45 years, Intercomp Company has been serving the weighing and measuring industry. We are the world’s largest manufacturer of portable weighing and measurement products, producing the highest quality products at competitive prices. Customers in aerospace, transportation, automotive, and numerous other industries know that Intercomp’s products provide reliable solutions for the most exacting applications.
Ensure Scale Accuracy with Intercomp
Contact your local Michelli Weighing & Measurement team of experts today. Whether you need portable scales or in-ground scales, we can help you find the right Intercomp equipment to help you ensure accuracy.